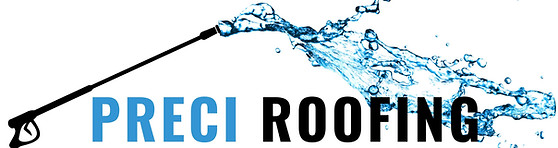
PRECI PAINTNG - OCCUPATIONAL HEALTH & SAFETY POLICY
ENSURING WORKPLACE HEALTH AND SAFETY
SAFETY POLICY 2013
Forward
This information has been designed to inform staff and visitors at Preci Painting Perth, of Workplace Health and Safety obligations (duties of care), to assist understanding of safe work procedures, and to help staff carry out duties in a responsible and safe manner. This material was developed by a working party of Preci Painting Perth. Contributions by the following people are acknowledged:
Zef (Preng) Preci (Managing Director/Operator)
Natalie Preci (Partner/Manager)
Rachelle Cohen (OH&S Administration Manager)
Director's Policy Statement
Preci Painting Perth recognizes their responsibility to provide a safe and healthy working environment for their staff, visitor’s clients and general public. This is achieved by:
A commitment to establish measurable objectives and targets to ensure continued improvement for the purpose of elimination of work related injury and illness;
-
A commitment to comply with OHS legislation and other requirements placed upon the company (including but not limited to WHS act and regulations, Electrical safety act, building and construction codes);
-
A commitment to formulate, document, maintain, communicate and periodically review this safety policy and control measures; and
-
Adopting standard procedures, based on occupational health and safety standards outlined in relevant legislation, compliance and advisory standards, and workplace policies.
Employees and visitors are encouraged to carry out their obligation to ensure the health and safety of themselves and others, and to support management efforts to implement workplace health & safety management strategies.
Legislation
The Parliament of Queensland enacted the Workplace Health and Safety Act (1995) to promote and protect freedom from disease or injury to persons caused, and risk of disease or injury to persons created, by workplaces, workplace activities and certain plant, and for related purposes.
The Workplace Health and Safety Act binds all persons (Section 4,) and applies to all workplaces, workplace activities and specified high-risk plant.
The Act:
-
Applies to everyone who may affect the health and safety of others because of workplace, workplace activities or specified high risk plant; and
-
Applies to everyone whose health and safety may be affected by workplaces, workplace activities or specified high risk plant
Obligations
Obligations of employers:
An employer has an obligation to ensure the workplace health and safety of each of the employer’s workers and any other persons is not affected by the conduct of the relevant person’s business or undertaking. (Section 28.)
Obligations of persons in control of workplaces:
A person in control of a workplace has the following obligations —
a) to ensure the risk of injury or illness from a workplace is minimized for persons coming onto the workplace to work;
b) to ensure the risk of injury or illness from any plant or substance provided by the person for the performance of work by someone other than the person’s workers
is minimized when used properly;
c) to ensure there is appropriate, safe access to and from the workplace for persons other than the person’s workers (Section 30.)
Obligations of workers and other persons at a workplace:
A worker or anyone else at a workplace has the following obligations at a workplace —
a) to comply with the instructions given for workplace health and safety at the workplace by the employer at the workplace and, if the workplace is a construction workplace, the principal contractor for workplace health and safety at the workplace;
b) for a worker — to use personal protective equipment if the equipment is provided by the worker’s employer and the worker is properly instructed in its use;
c) not to willfully or recklessly interfere with or misuse anything provided for workplace health and safety at the workplace;
d) not to willfully place at risk the workplace health and safety of any person at the workplace;
e) not to willfully injure himself or herself (Section 36.)
Discharge of obligations:
A person on whom a workplace health and safety obligation is imposed must discharge the obligation. (Section 24.)
Duty of Care and Negligence
Preci Painting Perth's staff has a duty of care to other staff and visitors during the course of their duties. A person not exercising this duty could be found negligent.
Generally the elements used to establish negligence and consequently liability are duty of care, breach of the duty and resulting damage or loss. If any of these elements is missing liability will not be established. Simply being in the same place as another does not mean that a duty of care is owed to that person. There must be a relationship requiring conformity to a standard of conduct to protect against foreseeable risk. The duty of care is breached by failure to conform to the standard.
Finally there must be some measurable damage or loss and a sufficiently close connection between the conduct and the resulting damage or injury. An injured party’s actions can contribute to the injury but this does not fully release the person owing a duty of care from liability.For example, an employee may ignore an instruction and be injured. While the employee contributes to the injury cause, the supervisor may still be partly liable for not taking reasonable steps to prevent the accident and subsequent injury from occurring. A supervisor owes a duty of care to an employee to protect the employee from any reasonably foreseeable risk of injury. While the standard of care expected is high it is not absolute and is not a duty of insurance against harm, but rather a duty to take reasonable care to avoid foreseeable risks.
Vicarious Liability
An employer is responsible for the actions of employees in relation to injuries caused to other employees or third parties. An act is within the course of employment if it is:
a) authorised by the employer and a lawful act;
b) authorised by the employer and an unlawful act — if the employer directs an employee to perform duties in a manner which involved the commission of an unlawful act (which includes, for example, breach of contract or other illegal acts), the employer may be liable to compensate any third party suffering loss or injury;
c) an unlawful method of performing what is otherwise an authorized act. Whether the employer is vicariously liable depends upon the facts of each case but, generally, the employer may be liable for acts committed by employees in the course of their employment.
NB: There is provision for personal fines in the Workplace Health and Safety Act, which cannot be covered by insurance.
Accident Reporting
Staff: If you are injured in an accident at work, obtain first aid treatment and notify you supervisor or manager. You will need to complete an Accident Report Form.
If you are admitted to hospital as an in-patient, the Division of Workplace Health and Safety must be notified on the prescribed form INCIDENT RECORD/REPORT.
Visitors:
If a visitor is injured on site
a) First aid should be administered;
b) Report the incident to the Preci Painting Perth host;
c) If the visitor is admitted to hospital as an in-patient, the Division of Workplace Health and Safety must be notified within twenty-four (24) hours;
d) Notify the section supervisor or manager or other relevant person.
Accident Investigation
All work injuries, work caused illnesses and dangerous events (including near misses) at the workplace should be investigated. The Workplace Health and Safety representative will investigate or assist in the investigation. Otherwise, the elected Workplace Health and Safety Representative will review the circumstances surrounding such injuries, illnesses or dangerous events, advise senior management of the results of the review and make recommendations arising out of the review.
ABSENCE THROUGH SICKNESS Notify the supervisor or manager as early as possible.
Certificates/Licences
If you are required to operate plant or equipment or drive motor vehicles you must have a current Certificate of Competency or a current appropriate driver’s licence.
Ensure that, if you have a Certificate of Competency or driver’s licence, it is current, and the administration manager has maintained a register of all licences.
Compressed Air
Serious injuries can result from the misuse of compressed air. Do not use compressed air for cleaning clothing or any other part of the body. If using compressed air to remove dust from a product etc. some form of eye protection must be worn, preferably goggles or a face shield. Turn off all valves after use. Pressure vessels over a certain size require registration and testing. Ensure that all vessels requiring testing are current before use.
Compressed Gases
Many gas cylinders look similar. The gas label on the cylinder is the only sure way to tell what gas is inside. Refer to the product information sheet for specific details on safe use, handling and storage procedures.
Construction Sites
Special consideration needs to be given to construction sites. All Preci Painting Perth personnel and contractors are to report to the principal contractor on site. In some circumstances, this may be the owner. (Domestic premises are an example.) The principal contractor must induct and supply a safety plan and discuss this with you.
Conselling and Disipling Procedures
Preci Painting Perth utilise a step-by-step approach to the counseling and discipline of all employees in relation to safety matters in order to ensure fair and just treatment of all employees and to protect the interests of all parties. Using violence, fighting or working under the influence of alcohol or drugs or serious and blatant breaches of safety rules and may be sufficient grounds for instant suspension and investigation.
CPR
Staff should be told the names of personnel who have received cardio-pulmonary resuscitation (CPR) training. All electrical personnel must ensure that their CPR and Switchboard Rescue certification is always current.
Damage Reporting
It is important that you report any damage you may cause or that you may become aware of your work area to your supervisor or manager.
Disposal
Disposal Of Chemicals
Only authorized persons are to dispose of chemicals or containers. It is the policy of Preci Painting Perth to support, where possible, environmentally friendly substances.
Based on current MSDS information, a supervisor or manager shall, and in accordance with safety and council regulations,
a) Check the label for advice on disposal of chemicals or containers.
a) Check the label for advice on disposal of chemicals or containers.
b) Triple rinse empty containers to remove all traces of the chemical.
c) Uncap, puncture and crush all rinsed containers.
d) Where possible return containers to the manufacturer or supplier; or ask your local
government what their requirements are for disposal. Do not burn.
Disposal Of Sharp Utensils Including Discarded Needles
Equipment:
a) Rubber Gloves
b) “Sharps” disposal container. This must be a resealable, puncture-resistant, rigid-walled container purpose built and labeled accordingly
Safe Disposal Procedures:
a) Take care not to prick yourself with the needle or sharp utensil.
b) Put on gloves.
c) Do not try to recap a needle.
d) Place the container on the ground next to the item.
e) If the item is a syringe with needle attached, pick up the syringe as far from the needle end as possible.
f) Place the syringe, needle point down in the container, and seal it with the lid.
g) Dispose of the sealed container according to local government refuse disposal requirements.
h) Wash hands thoroughly.
Drugs/Alcohol
a) Drugs must not be brought into the workplace.
b) Consuming alcohol is not permitted during working hours.
Electrical Equipment
Do not tamper with any electrical equipment no matter how minor the problem may be. Any electrical faults are to be reported immediately. Unqualified personnel must not attempt any repairs whatsoever. All portable electrical equipment e.g. radios, fans, computers, TV/s, Refrigerators, tools etc, are to be inspected, tested and tagged prior to use on site. This testing is to be maintained and recorded as per AS3760. All electrical equipment must only be connected to a suitable outlet protected by a suitably tested safety switch. All safety switches must have a current test certification and must not be used unless this certification is sighted. This applies to fixed and portable RCD’s. All portable equipment used on site must be connected to a suitably tested portable RCD or, if connected to a fixed RCD, the RCD is tested to AS3760 prior to use. Double adaptors must never be used at Preci Painting Perth premises or sites. Industrial quality extension leads of 1mm sq (minimum) must be used on construction or assembly sites.
Environment
The environment must be considered in all aspect of Preci Painting Perth operations. Consideration should be given to:
a) Correct disposal of rubbish, recycle where possible
b) Ensure all earth disturbance is shored against entering storm water drains.
c) There are no gasses released to atmosphere from gas bottles or refrigeration plant
d) Biodegradable materials are used where possible
e) Asbestos removal is carried out within the legislative guidelines
f) No undue noise is created
g) Internal combustion engines are to be regularly maintained to minimize emissions
Some environmental hazards that may be encountered but not limited to
a) poisonous or prickly vegetation
b) animals — domestic or native
c) venomous, stinging or biting insects
d) hot and dry conditions
e) cold conditions
f) contaminated water
Emergency Evacuation Procedures
Preci Painting Perth has procedures to manage all reasonably foreseeable emergencies. The procedures, including a map indicating evacuation routes, are made aware to staff when on site.
Hand Tools
The following rules should be observed when using hand tools:
a) Choose the correct tool for the job;
b) Make sure the tools you use are in good condition;
c) Use the tool as it was designed to be used; and
d) Store and carry tools correctly.
Harassment
Preci Painting Perth considers harassment in any form unacceptable behavior and will not be tolerated. This applies equally to any form of workplace bullying. Harassment and workplace bullying may also be unlawful. (e.g. Sexual or Racial comments). All allegations will be taken seriously and appropriate disciplinary action may be taken including referring to police or other authorities. Any employee experiencing alleged harassment must immediately contact a member of the management team.
Fire Extinguishers / Fire Blankets
All staff are required to familiarize themselves with how to use a fire extinguisher, and hose reels, and where they are located.
First Aid
All incidents requiring First Aid treatment must be reported to your supervisor or manager and the treatment recorded in the First Aid log book. When dressing wounds please be aware that any body fluid can be infectious. Ensure that cuts, abrasions, and open wounds on your own hands are covered with waterproof dressings to minimize the risk of infection. Disposable gloves must be worn where contact with body fluids occurs. However, if this is not possible, contamination should be washed off as soon as possible. Special care should be taken if spilt blood contains material such as broken glass. In such an event, the sharp material should be picked up with wadding, then wrapped securely in several layers of newspaper or put into some form of puncture-resistant container before disposal.
Hazard Reporting
Employees at the workface are in the best position to identify potential hazards. Employees are required to report actual incidents, near misses and hazards which have the potential to injure people or damage property. If the potential hazard is in need of immediate attention inform your supervisor or Workplace Health and Safety Representative.
Hazardous Substances/Chemicals
Some hazardous substances/chemicals that can be injurious to short or long term health are stored and used in and around the site. All hazardous substances/chemicals must be used strictly in accordance with directions! Ask your supervisor or manager for the Material Safety Data Sheet for any substance you use. READ IT CAREFULLY!
Housekeeping/Tidiness
Your cooperation and assistance is sought to keep your worksite as clean and tidy as possible with equipment being located in its correct location. You can assist by keeping your work area, aisles, stairways, conveniences, lunch rooms, locker room etc. tidy and free of unwanted materials. Report all hazards if you can’t correct the situation immediately. Passageways and access routes must not be obstructed in case of emergency (fire etc.) A clean and tidy workplace is a safer place to work.
practicable. An incident report should be filled out and filed.
Infectious Diseases
You should ensure that you have adequate immunity to measles, mumps, rubella, poliomyelitis, diphtheria and tetanus. Immunity to rubella is particularly important for female staff of child-bearing age. Vaccination for Hepatitis is recommended. If you become aware of a case of an infectious disease, notify your supervisor immediately as it may be or may result in a work related illness which is required to be reported under the Workplace Health and Safety Act. In cases where someone chooses to divulge this information, staff must respect this confidentiality. Education programs about infectious diseases and infection control procedures will reduce fear, anxiety, prejudice and alienation. Disclosure of such confidential information may lead to reluctance on the part of other individuals to divulge their infection status.
Isolation Procedures
Isolation procedures are necessary to maintain a safe working environment for you and your workmates. The company lockout procedure and policy must be adhered to. Personal or supervisors “do not operate” tags and padlocks must be used prior to working on equipment ‘Out Of Service’ tags and lockouts should be placed on plant machinery or tools that are out of service for some reason. Plant machinery or tools displaying out of service tags and lockouts should not be used. The electrical safety act requires that personal locks be used when working on electrical apparatus.
Ladders
Aluminium or other metal ladders must not be used where an electrical hazard exists, and lights must be switched off before changing globes etc. All ladders are to be labeled and listed on a register and maintained to AS1 892
Machinery
No equipment is to be operated without the appropriate guarding in place. Equipment requiring a licensed operator cannot be used by personnel who are not licensed and authorized to do so.
Manual Handling
Careless lifting and carrying can cause serious injury. Think before you lift and observe the following precautions.
Materials Handling
Whenever practical, heavy lifts are to be made by mechanical means. If manual handling is unavoidable:
a) Size up the load and seek help or use a lifting aid if necessary.
b) Position the feet correctly, as close as possible to the object to be lifted.
c) Bend knees and get a good secure grip.
d) Take a deep breath, keep your head erect and lift by straightening your legs.
e) Keep your back straight, your arms in and your elbows and knees slightly bent.
f) When carrying a load, hold it close to the body and avoid twisting the back.
g) When lowering a load, follow the procedure in reverse keeping the back straight.
For lifting, lowering or carrying loads —
a) in seated work, it is advisable not to lift loads in excess of 4.5 kg;
b) evidence shows the risk of back injury increases significantly with objects above the range of 16-20 kg. Therefore from the standing position, keep the load below or within this range;
c) as weight increases from 16 kg up to 55 kg, the percentage of healthy adults who can safely lift, lower or carry the weight decreases. Therefore, more care is required for weights above 16 kg and up to 55 kg in the assessment process. Mechanical assistance and/or team lifting arrangements should be utilised to reduce the risk of injury associated with these heavier weights; and
d) generally, no person should be required to lift, lower or carry loads above 55 kg, unless mechanical assistance or team lifting arrangements are provided to lower the risk of injury.
MATERIAL SAFETY DATA SHEETS (MSDS’s)
A copy of all MSDS sheets shall be kept for all substances held by Preci Painting Perth. No substance shall be delivered to Preci Painting Perth’s premises or sites unless there is an MSDS provided to Preci Painting Perth staff prior to delivery. An MSDS has information on using and storing chemical products and substances safely.
Different chemicals or substances can cause different health problems. They also have different safe use requirements. For these reasons it is important to know about the chemicals and substances used at your workplace.
An MSDS gives advice on:
a) the ingredients of a product
b) the health effects and first-aid instructions
c) precautions for use
d) safe handling and storage information
e) Staff are required to read any relevant MSDS.
Medication
The following procedure should apply for employees needing to take prescribed medication while at work:
a) The medication must be clearly labeled with the persons name and administration requirement.
b) The medication must be safely stored.
c) There must be no adverse effects that could cause the person to injure themselves or others.
d) The employees’ supervisor or manager must be informed before any medication is brought onto company property. Including company vehicles.
e) The name and contact details of the prescribing physician must be clearly identified on the label or given to the employees supervisor or manager.
Mobile Equipment (including mechanized lifting machinery)
Only authorised and certified personnel or authorised and certified Contractors are allowed on any item of plant requiring a Certificate of Competency to operate. Any employee or non-employee who uses mobile equipment provided by an employer has a duty of care to act in a manner that does not adversely affect the health and safety of themselves or others at the workplace.
Motor Vechicle Safety
Often a motor vehicle and its driver are the most visible part of an organisation to the public. The driver’s safety, the public’s safety and potentially the reputation of the company rests with the motor vehicle driver. Staff driving motor vehicles in the course of their employment must hold a current licence to operate the particular vehicle and are required to observe all applicable traffic laws and to drive carefully in all circumstances.
a) Any vehicle defect must be reported as soon as possible. Smoking is not permitted in any vehicle
b) The Road Use Management Act (QId) must be abided at all times.
c) When refueling, the engine must be switched off and mobile phones are not to be used.
d) All trailers attached to a vehicle are suited to the towing capacity of the vehicle and be properly attached. All safety chains are attached and lighting is functional.
Office Safety
The most frequent types of office accidents are falls, strains, cuts and electrical shocks. To avoid injury there are a number of guidelines, which need to be followed in your office:
a) Any electrical defects in cords or machines must be repaired by a qualified electrical worker.
b) Avoid having telephone and electrical cables across aisles and passageways. No lead shall pass through a doorway.
c) Serious strain can result from improper handling of boxes, office supplies, files and office machines. Use trolleys where available and lift with a straight back and using the more powerful leg muscles. Get help where necessary.
d) Watch out for recently polished floors and wipe up any spills immediately.
e) Open one filing cabinet drawer at a time to prevent it tipping over.
f) Do not leave desk drawers open.
g) Doors should be opened slowly to avoid striking anyone on the other side.
h) Material should not be placed on top of cupboards or other places where it could fall.
i) Always use handrails when going up or down stairs.
j) Staple or clip papers together. Do not use pins.
k) Keep unsheathed knives or other sharp objects in a separate container in desk drawers.
l) Hand operated guillotines must be left closed when not in use.
m) Heating appliances, e.g. ovens and room heaters, must be switched off and unplugged when ceasing work.
n) Learn the fire and evacuation procedures for your building. Never use lifts in a fire situation.
o) If you need to climb, use a step stool or a ladder — never stand on wheeled or revolving chairs.
p) Set adjustable chairs and tables at a comfortable working height. Inspect your chair regularly for defects.
q) Report loose and defective floor coverings immediately.
Personal Protection Equipment (PPE)
PPE is provided to control hazards and maintain your health and safety. Where PPE is provided it must be worn. All PPE must conform to the relevant Australian Standards.
All employees are responsible to ensure that they use PPE as required for the tasks.
Hand Protection: Appropriate approved gloves must be worn for various tasks. Hand lotion is provided for when required.
Hearing protection: Appropriate hearing protection must be worn if the noise is excessive or continues for long periods. At no time are portable entertainment devices permitted to be worn in the ears or around the neck whilst at work.
Footwear: Safety boots must be worn in workshop or site areas. Fully enclosed footwear is the minimum standard in all other areas. No thongs, sandals or high heel shoes are permitted at a workplace. (this includes a motor vehicle)
Head protection: In areas of food preparation or as directed by the principal contractor or in areas where there is a risk from falling objects, suitable head protection must be worn.
Visibility clothing: High visibility clothing is encouraged within the working environment. High visibility clothing must be worn on all construction sites and around moving machinery (cars, forklifts in a loading dock)
Welding shields: Welding shields and screens must be used when welding or grinding
Rehabilitation
Preci Painting Perth is aware that effective occupational rehabilitation is in the best interests of the individual staff member from both a social and economic perspective, where sustained injury or illness is work-related. Preci Painting Perth encourages an early return to work using alternate selected duties as part of the rehabilitation process, where this is possible, under the direction of the treating medical practitioner.
Risk Management
Preci Painting Perth adopts a risk management approach to Workplace Health and Safety.
Basic Steps in Risk Management:
STEP 1: Identify the hazards
STEP 2: Decide who might be harmed and how
STEP 3: Evaluate the risks and decide whether the existing precautions are adequate or whether more should be done
STEP 4: Record your findings
STEP 5: Review your assessment and revise it if necessary
Safety/Road Signage
Safety signs, warning and road signs are appropriately placed for your protection. It is part of employees’ duty of care to comply with all speed, parking, information and industrial signs. Suitably trained and licensed Traffic Controllers are the only persons permitted to place signs or direct traffic on a carriageway. (this includes a footpath)
Smoking
Preci Painting Perth maintains a smoke-free environment in all buildings and enclosed areas. Smoking is also not permitted within 4 metres of a doorway or within 10 metres of an area frequented by children. Preci Painting Perth encourages a non-smoking environment in the external areas. Smoking in the workplace is strictly prohibited for persons while handling chemicals, herbicides or pesticides, whether within buildings or in the grounds.
Supervision
‘Supervision’ refers to any situation where managers, supervisors or leading hands, in the execution of their formal or informal duties direct, oversee, watch over and are responsible for employees during the performance of, or operation of, their duties. Staff supervising employees owe a duty of care to those employees.
Sun Safety
Employees are provided with and expected to wear a hat with a broad brim 10-12 cm wide while working outdoors. Staff are encouraged to wear suitable clothing and 15+ (as a minimum) broad spectrum sunscreen and sunglasses where appropriate to minimise the damaging effect of the sun on the skin and eyes.
Drink water regularly to prevent dehydration
Training
Training in health and safety will be provided as needs arise and are identified.
Suggestions for training programs should be made to your supervisor or Workplace Health and Safety Representative.
Workplace Health and Safety
Compulsory safety meetings are conducted “at a nominated frequency”. These meetings are a positive way of addressing health and safety issues and implementing control measures in a timely manner. There shall be regular safety audits/inspections made to ensure that all procedures and facilities remain in a safe condition. These audits and observations are filed and discussed at the safety meetings.
Workplace Health and Safety Representative
The staff members may elect a workplace health and safety representative on their own initiative or at the employer’s suggestion. If the staff members decide to elect a Workplace Health and Safety Representative for the workplace, the staff members must tell their supervisor or manager of the decision.